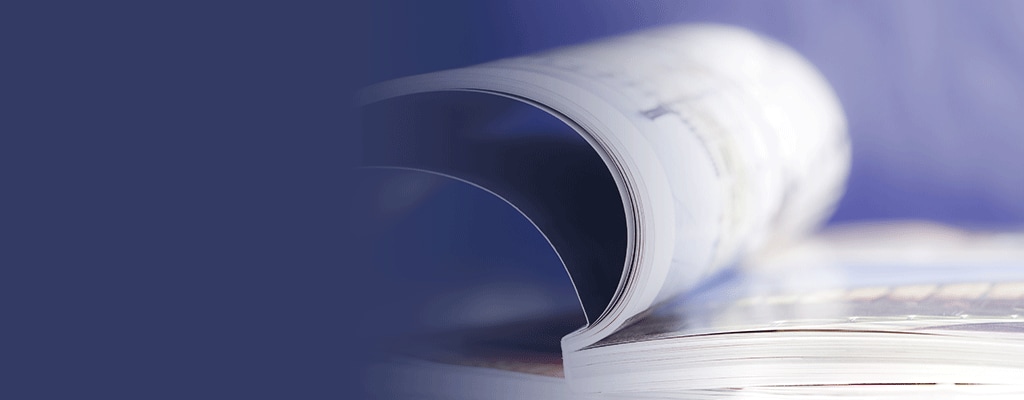
Trend Insight
LVDT Terminology
Understand the terminology used to specify a Linear Variable Differential Transformer (LVDT) position sensor.
Key Terms
Read the following seven key terms and learn how they apply to selecting an LVDT position sensor.
Nominal Linear Range
The basic variable in LVDT selection is the maximum range of core motion, which produces an analog output of specific linearity. Full-scale displacement is the distance a core can travel from its null position in this linear region. Since the core can be displaced from null toward either end, the linear operating range is twice the full-scale displacement. When stated as plus or minus (+/-) full-scale displacement is referred to as the nominal linear range. When stated without a polarity, it is called the LVDT's full range, full stroke or total stroke. The nominal linear range of any LVDT varies with frequency. When the LVDT is used with the correct core for the specified frequency, the actual linear range will always equal or exceed the nominal value. When optimum linearity is not essential in an application, the practical operating range may extend well beyond the specified nominal linear range. Nominal linear range is specified for a high impedance load, typically 50kOhm to 0.5MOhm. A low load impedance can have a deleterious effect on linearity and nominal linear range.
Linearity Error
As LVDT output is a nominally linear function of core displacement within its linear range of motion, a plot of output voltage magnitude versus core displacement is essentially a straight line. Beyond the nominal linear range, output begins to deviate from a straight line into a gentle curve. From a statistically best-fit straight line versus core displacement within an LVDT's nominal linear range, the maximum deviation of LVDT output is defined as the linearity error or the non-linearity of the LVDT. Linearity error is typically expressed as +/- a percentage of full-range output or in terms of an error band width that envelopes the straight line and deviations. The proper interpretation of linearity error for an LVDT depends on the ultimate application on the LVDT in a measurement application. Some users use non-linearity as a measure of system accuracy as it is often the largest error.
Full-Scale Output
FSO
For an AC-LVDT, full-scale output is the output of an LVDT with its core positioned at full-scale displacement and with its primary excited at a specified nominal input voltage. In most cases, though, a better way to compare AC-LVDTs of the same linear range is through sensitivity. Sensitivity is usually specified in terms of milliVolt output per thousandths of an inch core displacement per Volt of excitation (mV/mil/Volt). Sensitivity varies with excitation frequency, which must also be specified. Sensitivity mostly affects the gain required of the LVDT's signal conditioning electronics. For most DC-LVDTs, the comparable characteristic to sensitivity is scale factor, which is usually expressed as Volts DC output per inch of core displacement. Some legacy DC-LVDTs use a ratiometric configuration, which requires that they also use the same units as sensitivity, or have their scale factor specified for a particular DC input voltage. There are also DC-LVDTs whose output is into a 4-20mA current loop, so their scale factors are expressed as milliamperes per inch (mA/in) or milliamperes per mil (mA/mil).
Resolution
Resolution is the smallest core position change that can be observed in LVDT output. An LVDT's resolution is essentially infinite as it operates on the principle of magnetic coupling. An infinitesimal change in core position will produce an output change. In practice, the limitation on system resolution is the ability of the associated electronic equipment to sense the change in LVDT output, which is called the signal-to-noise ratio of the system. With a properly designed LVDT measuring system, microinch resolution is not uncommon.
Repeatability
The ability of a sensor to reproduce the same output for repeated trials of exactly the same input under constant operating and environmental conditions are the single most important factor for sensor selection. Called repeatability, this parameter is the only irreducible and uncorrectable source of static error in any electromechanical measuring system. Repeatability error is the limiting factor in making any sensor-based measurement. A well-made LVDT is so repeatable that it is affected only by the mechanical factors of the physical members or structures to which the LVDT's core is attached and to which the LVDT's coil is mounted. Both repeatability and resolution contribute to overall measurement error, and are usually expressed as a percentage of full-scale output. These parameters apply equally well to AC-LVDTs and DC-LVDTs.
SEALED VERSUS VENTED LVDTS
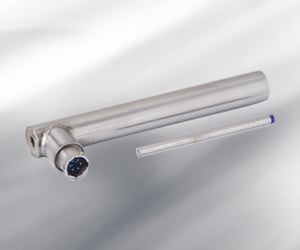
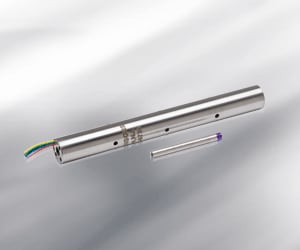
Sealed LVDT
A sealed LVDT prevents any liquid or gas from entering the housing of the sensor. For applications where corrosive/pressurized media, high humidity or radiation are present, a hermetically sealed LVDT is recommended to confirm outside media does not enter the windings. This sealing makes sensors impervious to dirt, water, steam, chemicals, and even extreme temperatures that can shorten its life or reliability. In this configuration, the heavy-duty housing, bore liner and end washers of the LVDT are welded together to form a hermetic seal. Typically, hermetically sealed LVDTs can withstand operating pressures up to 3000 psig. The hermetically sealed construction also lets the core withstand temperatures up to 400°F.
Vented LVDT
To accommodate extremely high pressures, the sensor case can be vented to equalize pressure inside and outside the LVDT linear position sensor. Vented versions of LVDTs can withstand a combination of high pressure, temperatures, shock and vibration. However, since vent holes exposing the coils inside the housing, any fluid in which the LVDT is encompassed must be electrically non-conducive and chemically benign. Vented LVDTs can operate in temperature extremes of -65°F to +400°F (-55°C to +200°C) and operating pressures of 35 kpsi. High temperature ratings are achieved using internal materials rated for these temperatures.